2019
Pioneer Asia Group
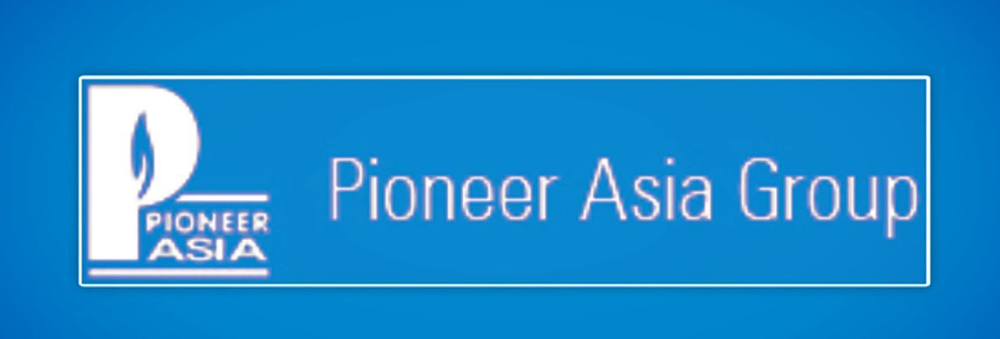
The customer
The client, Pioneer Asia had its small beginning in 1945. It has grown well with times and has adapted to mechanization. The group today is the Second largest manufacturer of safety matches in India producing more than 10 Million match boxes per day.
The group has also established wax matches factories in Sri Lanka, Nepal, Madagascar, Kenya and Tanzania.
Under The Match Makers brand, they manufacture Fancy Matches in various sizes and designs and meet 95% of the requirements of hotels in India.
The company has expanded its reach across the traditional retail and modern trade channels and has a strong network of over 2000 distributors & agents.
Industry: Matches manufacturing
Number of employees: 10,000
Revenue Rs. 700 crores ($100 million)
Locations: 50
Customer since 2009
Challenges
Client was having custom made programs for logistics and finance. There were many challenges right from Order Tracking till maintaining BOM across all factories. Order execution was having huge delay due to lack of visibility of correct inventory status across all locations. Wages calculation for workers was taking much time which had an impact on disbursement of wages. Since both export and domestic orders has to be tracked for delivery, without a proper integrated system it was complicated.
Moreover, many of their processes required customization
Solution
Profit Plus ERP software provided the client a real-time access to sales and inventory data. Profit Plus’s capability to customize quickly were capitalized and fulfilled all of their customization requirements. The MRP module implementation gave them the real-time visibility to run the business.
The cloud based integrated solutions covers Sales, Purchase, Inventory, Finance, Import, export, MRP, Production, Payroll, and Taxation, connecting multiple locations, factories and depots. It further ensured quicker report generation, timely availability of information and eliminated manual data consolidation in excel sheets.
Benefits
- Standardization of BOM across all factories
- MRP has empowered the purchase process to implement JIT concept and reducing the stock level to a great extent
- The cycle time of order to delivery is reduced and tracked with clear visibility to management.
- Able to arrive at accurate costing. Material and process cost at each WIP level and finally at the end product level
- Wages calculation time has been reduced drastically
- Wastages are properly tracked at each process level and actions have been taken to reduce it
- Since all their business happening across the geographies are on the dashboard of the management, they have complete control over the business now.
Customer speak
“The Auvit BPA tool helped us to make lots of customization in shorter span of time and with minimal cost”